SHINTO Tile Manufacturing Process
Tile Manufacturing Process
We currently manufacture our tiles using a tunnel kiln, the standard practice for ceramic tile manufacturing.
Each session is controlled using the latest technologies.
Blended clay

Main supply unit
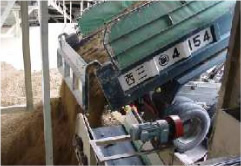

Temporarily holds clay as it supplies clay for the next process.
Sub supply unit

Kneading machine
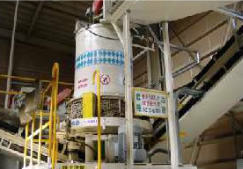

This is where clay is kneaded to make it uniform.
We inject steam to improve molding performance.
Extruder
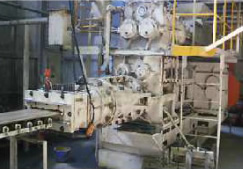

By turning the air inside the clay into a vacuum, we remove it and create a form close to the product itself (called araji).
Cutting Machine
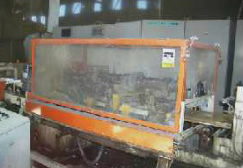

The continuously fed araji are cut into individual pieces.
Press
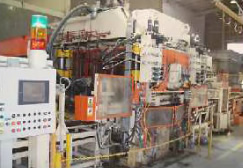

The clay is formed into the product shape.
Drying furnace
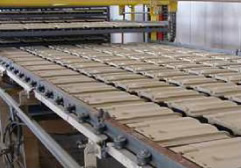

Clay contains roughly 20% water, so this process removes that water.
The dried tile is called shiraji.
We use excess heat from the tunnel kiln as the heat source for this process to save energy.
Glaze

Glazing
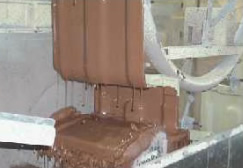

Firing machine (tunnel kiln)
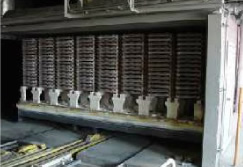

The tiles are fired at temperatures of up to 1120°C.
The glaze is also colored during firing.
Screening inspection of all tiles
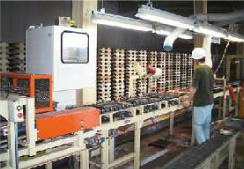

All tiles undergo a visual inspection.
Defective tiles are removed and sent to be recycled into blended clay.
Palletizer

Stretch packing
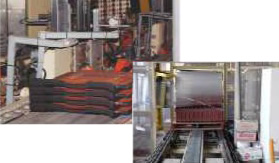

Tiles are bound in packs of four using PP bands, and loaded onto pallets in predetermined lots.
They are wrapped in film for storage.
Finished products
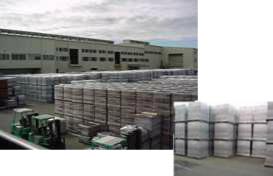